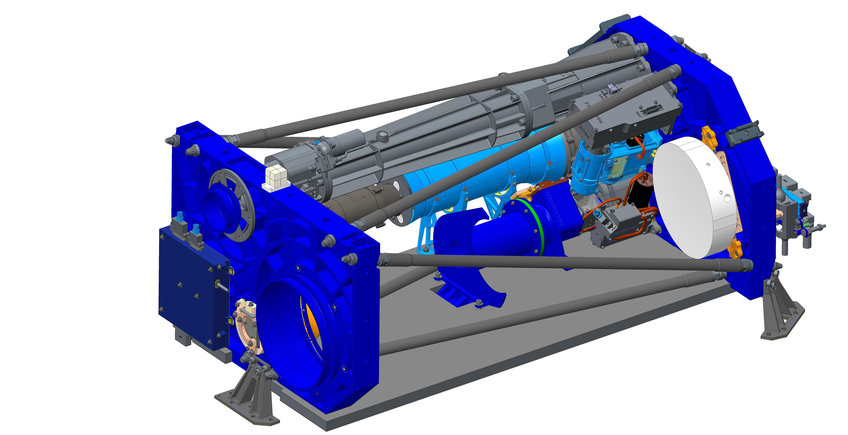
Mechanical Development & Design
The mechanical development supports instrumental projects of the scientific departments in the areas of design, structural analysis, system engineering, project management, testing and integration.

As a rule, collaboration on instrument construction begins with the first concept studies and developments, which are visualised at an early stage with the help of powerful 3D design software.
Contribution to instrumental projects usually begins with initial concept studies and developments, which are visualized already in early phase using powerful 3D design software.

Structural Analysis
Using various modelling and simulation software suites such as FEM/FEA (Finite Element Method or Analysis), the designed structures are examined and optimized to prevent failure during rocket launch or to meet the rigorous requirements of a mission within the solar system. To achieve this, our structural engineers typically employ modal- (natural frequency), random and shock analysis.

Thermal Analysis
To ensure that highly accurate measurement principles and scientific instruments, along with sensitive electronics are functional under space conditions (mission-dependent ranging from -150 to +200°C), our thermal engineers simulate and optimize the designed structures, surfaces and coatings in collaboration with international project partners.

Opto-Mechanical Analysis
The STOP analysis represents a combination of results from mechanical, thermal and optical analyses. This process integrates outcomes from various calculation disciplines into optical simulations, allowing predictions on the performance of optical instruments e.g. in terms of image focus, pointing stability or other disturbances and reveals optimisation potential.

Mechanisms
The conception and design of precision mechanisms for our scientific instruments in the space sector requires greatest diligence, as they have to operate reliably in the extreme environment of space. When designing such mechanisms, high-quality materials and special lubrications are used to withstand the high stresses and extreme temperatures of space about mostly long durations.
The engineers and technicians involved in the development of these precision mechanisms must adhere to the highest standards and stringent safety requirements to avoid or mitigate potential impacts of failures onto the instrument (e.g., through the implementation of fail-safe mechanisms).